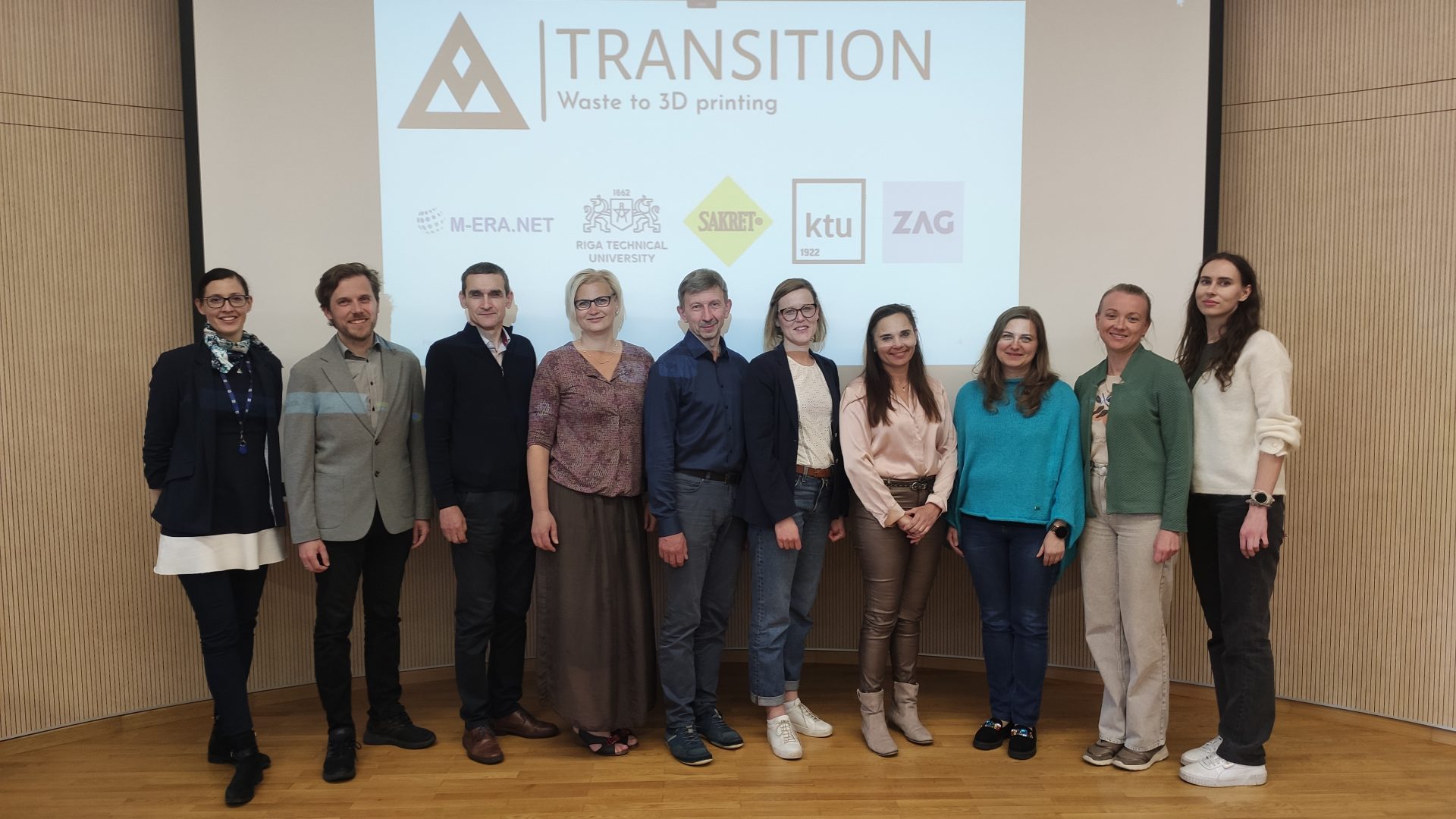
In May 2024, as part of the M-ERA.NET project “TRANSITION,” project team from RTU and SAKRET had the opportunity to visit our project partners at the Slovenian National Building and Civil Engineering Institute (ZAG) in Ljubljana, Slovenia. The goal of this visit was to share knowledge on the tests conducted so far and to align our research goals and future ideas. For some of the team, the visit was planned for a few days longer to carry out 3D printing and fresh concrete tests that could only be done at ZAG.
PART I PRESENTATIONS, DISCUSSIONS AND FUTURE PLANS
On the first day Project leader M. Sinka briefly summarized all the dissemination activities carried out within the framework of this project so far. Regarding dissemination, he also introduced everyone to the student competition planned for the following months. We had a brief discussion about this, and we concluded that this competition could easily be made international so that students and representatives from all the institutions participating in TRANSITION project could apply.
Within the framework of this project, it is planned to create a large-scale object – LabLab astronaut – for which we already printed a smaller-scale prototype this winter. Even though the architectural design for this object is somewhat finished, there is still a need to develop the technical design. The technical design would include solutions for assembly, detailed drawings, 3D models, and other elements. This is where the student competition comes in. The idea is that each student group would be assigned a mentor to help realize their ideas for technical solutions and their execution. At the end of the competition, the best group will be rewarded with a prize.
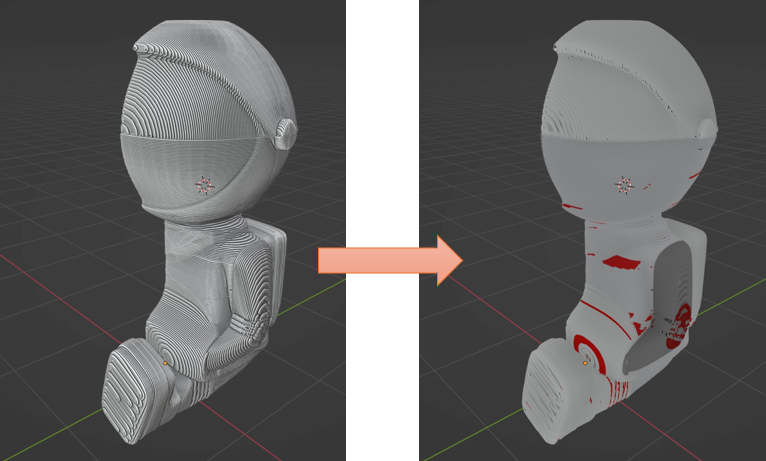
3D model of the LabLab astronaut
Later on this day we continued on with the meeting. Each project partner presented their latest work and progress. This was very important to discuss and understand in which directions to conduct further research. For example, when RTU presented their newly acquired disintegrator, it initiated a discussion on the potential for milling ashes in a wet state, which could be an interesting direction to explore.
G. Sahmenko from RTU introduced the rest of the project participants to the mechanical properties of preliminary mixtures. Based on these mechanical properties, optimal mixture proportions for a trial mixture for 3D printing has been developed. So far this trial mixture has been printed out once and from that it was concluded that particle packing needs to be improved. Based on everyone’s experience, it was discussed which materials, either microsilica, finely milled limestone or others, would be the best additives in this case. A. Sapata shared her experiences with various fresh mass property tests, such as unconfined uniaxial compression test, squeeze flow test, mini cone test, and slugs test. Some of these tests will be incorporated into our plan for determining fresh mass properties later in the week. B. Migliniece from SAKRET reported about works completed from their side, ZAG reported on their work.
At the end of this day we had a guided tour through Ljubljana. This was not a tour for the regular tourist, but more like a detailed explanation of how the architect Jože Plečnik (1872 – 1957) and his descender Edvard Ravnikar (1907-1993) participated in the creation of the landscape of this city as it is now. The guide introduced us to some apparently very well-known architectural landscaping ”tricks” that these architects used in their work, such as playing with perspective and geometric forms to create illusions, outline specific buildings, and create the overall view.
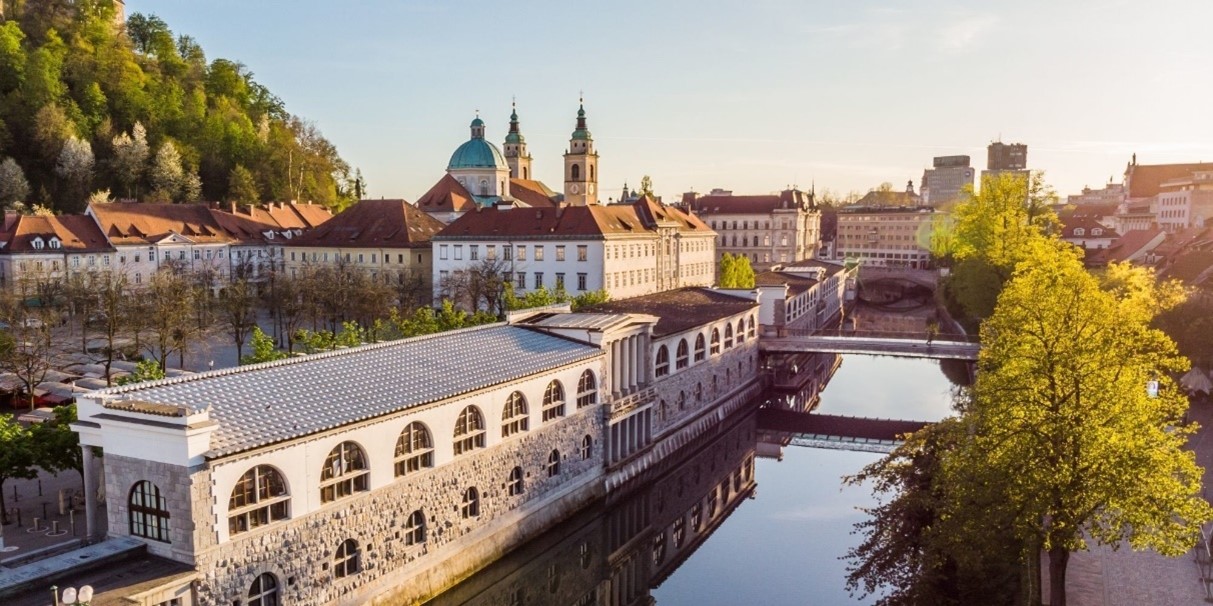
The Ljubljana Central Market by Joze Plecnik.
On the second day of our visit, we started out with a laboratory tour. We were introduced to both new tests and some new colleagues. Particularly interesting was the small concrete press used to compress cubes 2x2x2 cm. The laboratory workers also shared some tips and tricks for everyday work in a concrete laboratory. They suggested that it is better to use silicone molds for geopolymers but leave the metal ones for cement. They showed us how they store their equipment, how accurately they mould samples so that highly precise results can be obtained even from very small samples, and showed us how to correctly perform tests, for example, the LeChatelier test.
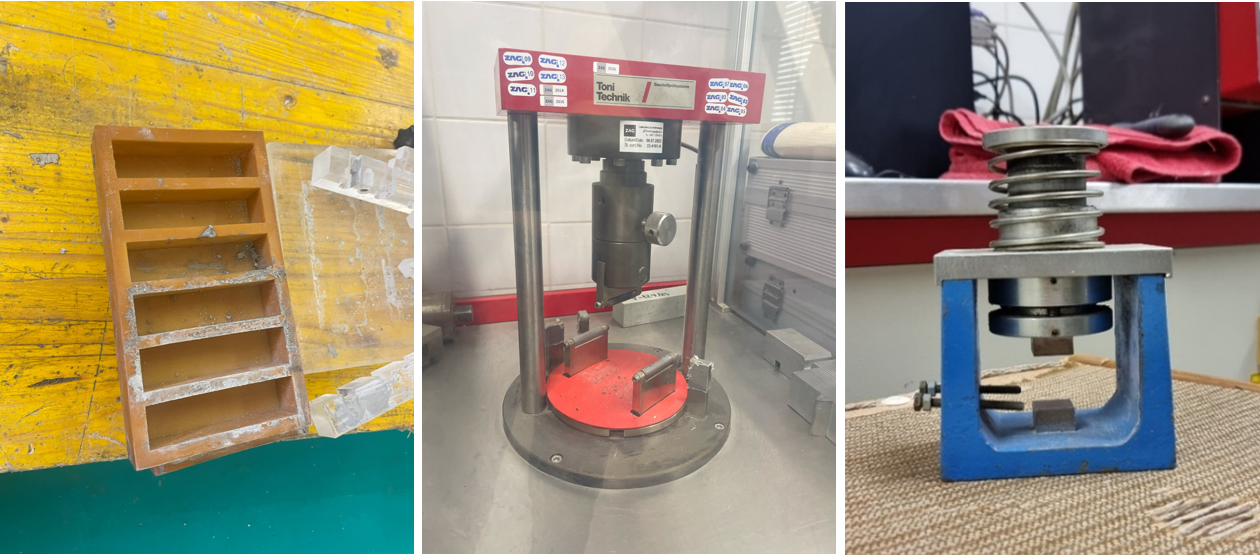
From the left: silicone moulds for small mortar prisms; flexural strength device; a self-made compressive strength device for samples 2x2x2cm.
All of the ZAG’s guests were introduced to the 3D printing laboratory and some of the objects that had been printed out so far. Particularly interesting was the rope-like texture of the printed concrete objects that is created by the 3D printer.
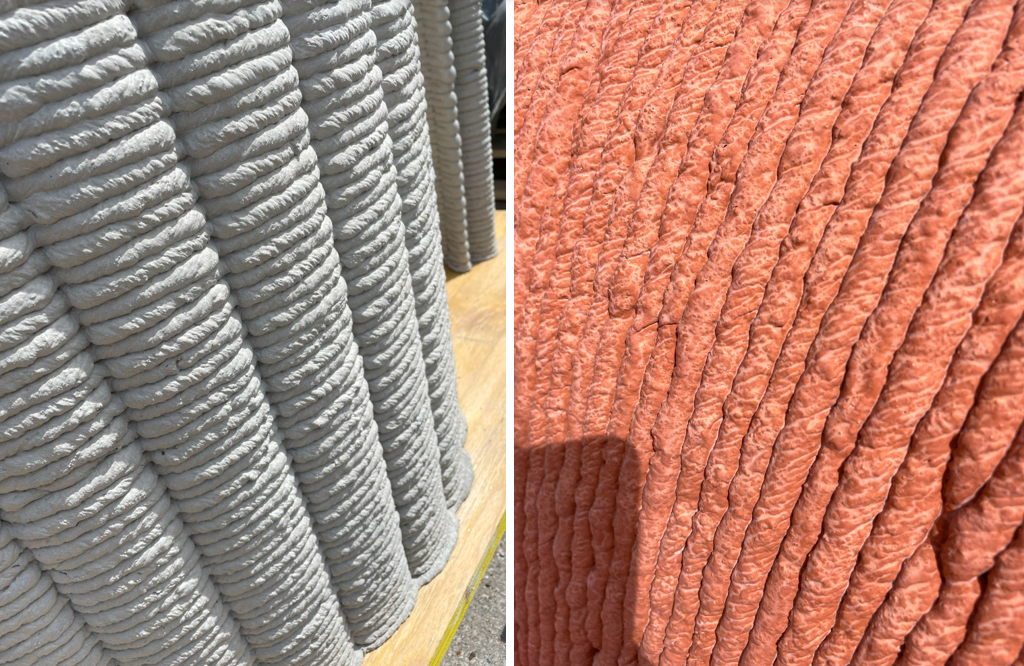
Texture of the printed objects.
After lunch, we had a discussion on the development of a small-scale prototype for 3D printable concrete mixes. L. Hanzic led the presentation on the key geometric features and parameters necessary for the prototype, considering the limitations of different printer types. Afterwards, K. Ster presented how ZAG has organized our project data on the open-access server, OSF, ensuring transparency and accessibility. The main takeaway from this was the importance of data storage so that information can be easily accessed even five years from now. We know this is a struggle for many.
Thus far, we have obtained and processed data for only one type of raw ash. However, there are three additional types of ashes that we haven’t worked with so far: Auvere electrostatic filter ash, Auvere bottom ash and Enefit 280 ash, both disintegrated and raw. During this discussion, we decided which raw material tests need to be conducted so that we can compare all the ashes and make conclusions on their suitability for use in concrete composites for 3D printing.
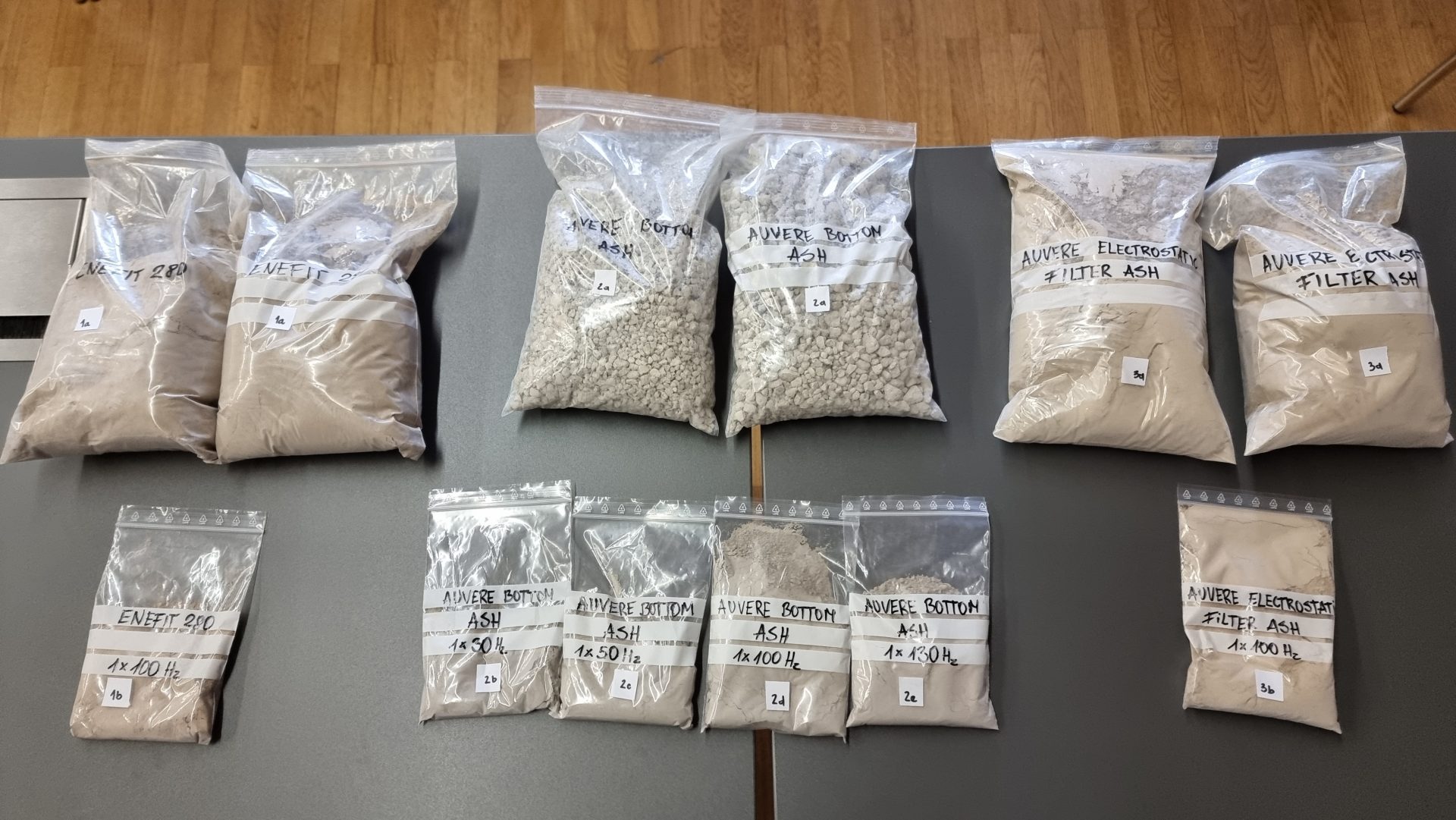
Different types of ashes
On the third day, we had multiple individual meetings to discuss specific problems and questions that have not been addressed so far or are too complex to be addressed in online meetings.
All of the presentations and discussions were not only informative but also inspiring, providing us with new ideas and approaches for our project. This project is not just about researching and analyzing the properties of raw materials and developing mixtures; it is also about storing data, sharing knowledge through scientific articles, and promoting 3D printing through competitions, thereby involving new people in the field. Alongside all these processes, we came up with new ideas that we will try to include and explore, and even if they are unsuccessful, we will definitely learn a lot from them.
PART II 3D PRINTING AND TESTING
The plan for the final days was to carry out 3d printing and fresh state tests on ready-made mixture for 3D printing. Before starting, we discussed in detail the plan for the following days. Various fresh state tests were planned, such as the Slugs test, unconfined uniaxial compression test, Vane test, rheometer, ultrasound test and hardened state compressive strength tests as well. The main goal of each test was to determine yield stress at different time intervals: 5min, 15min, 30min and 50min.
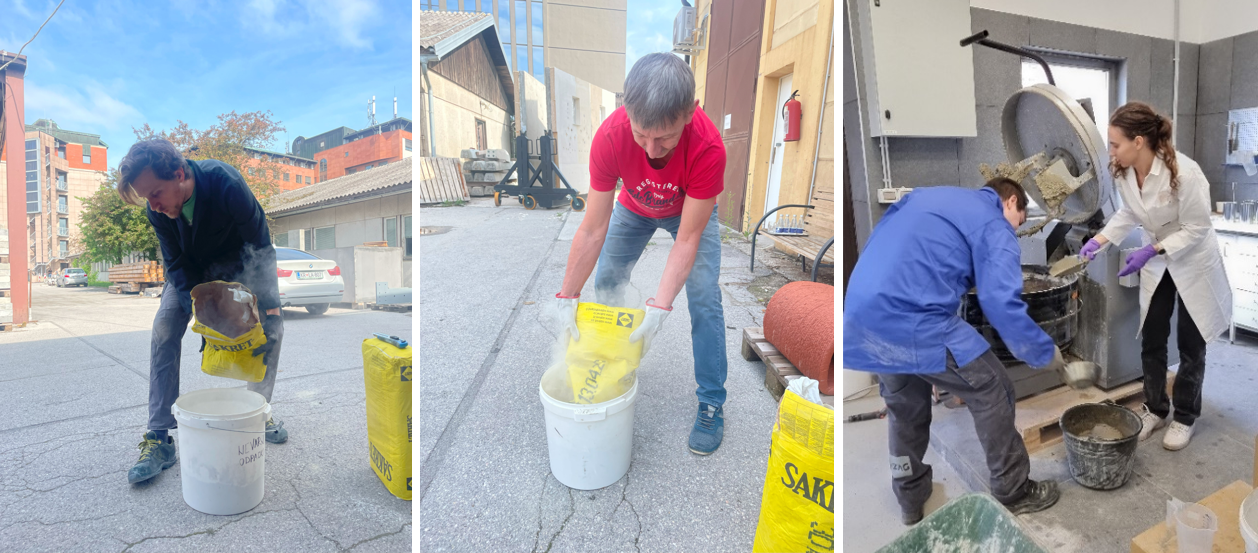
Preparation process for 3D printing.
First, the Slugs test was performed. This is a relatively new test method that helps determine the approximate yield stress of extruded materials. The test is based on measuring the mass of slugs extruded through a 3D printer. Depending on the length and the weight of each slug, it is possible to determine the material’s yield stress using the formula. This test was already performed at RTU using their portal-type printer and the same ready-made mixture for 3D printing many times before. It was interesting to find out that the same mixture showed the same yield stress when carrying this test out on the completely different 3D printed in ZAG.
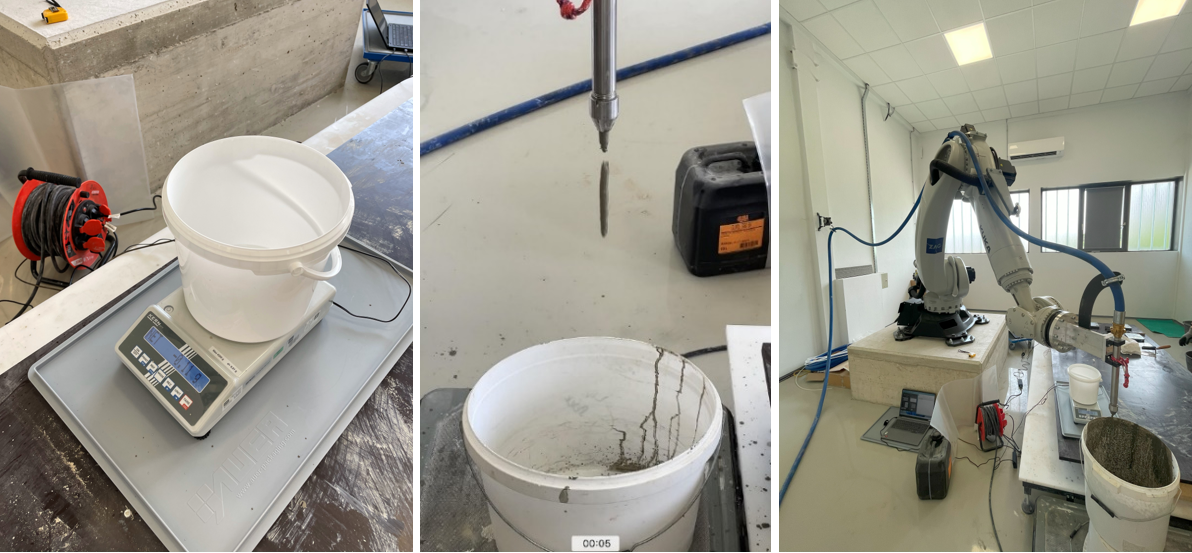
The Slugs test.
The unconfined uniaxial compression test allows to determine the compressive strength, yield stress, and the modulus of elasticity of fresh concrete at different ages. Additionally, using the results of this test, it is possible to determine the rate at which these parameters change over time.
For this test, the chosen sample size was H=100mm and D=50mm, maintaining the ratio of H/D=2. This size was selected as optimal after performing multiple test trials where it was concluded that it best represents the printed object dimensions. If smaller samples are used, they are significantly affected by pores and voids formed during molding, while larger samples are more influenced by gravitational forces – due to higher vertical stresses, they tend to spread more laterally. Molds composed of two half-cylinders were used to minimize lateral deformations during demolding.
Since compression samples have a very small compression area and the material has very low compressive strength in its initial stage, a highly sensitive apparatus is required. This apparatus must be capable of precisely reading deformations and the applied load value. For this reason ZAG and KROKK had developed a small, portable compression apparatus with a load cell capacity of 500 N. The frame consists of four posts to which a sliding load plate and fixed electronics plate are attached. Specimens were cast directly onto a reaction platform. The platform is not moved so that the specimen is not disturbed before the test.
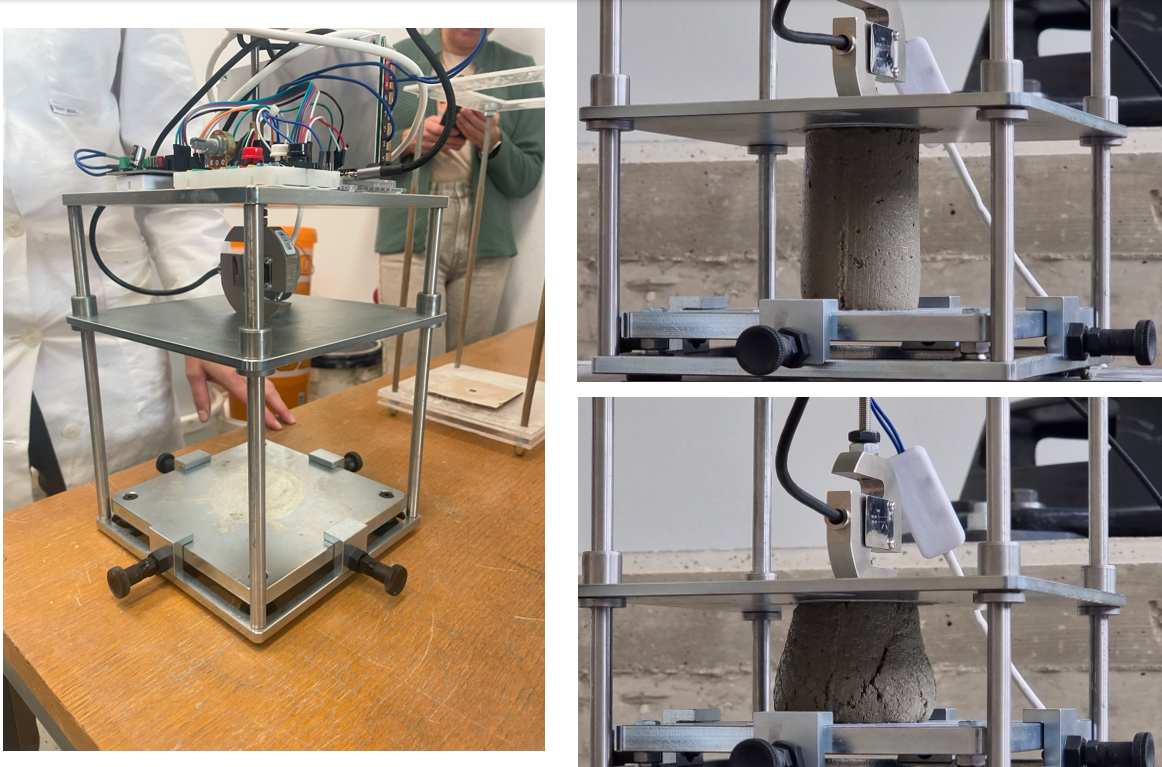
On the left: compression apparatus developed by ZAG and KROKK. On the right: samples before and after the compressive strength test.
Vane test comes from soil mechanics and is used to obtain shear strength of a cohesive soil. The used Hand Vane Tester comprises of four blades making 90º to each other and a torque head with a direct reading scale which is turned by hand. The Vane device was inserted inside each sample to a constant depth. While holding the sample firmly, rotation of the vane was initiated mechanically and rotated until a maximum torque value is obtained. At this point the yield stress is recorded.
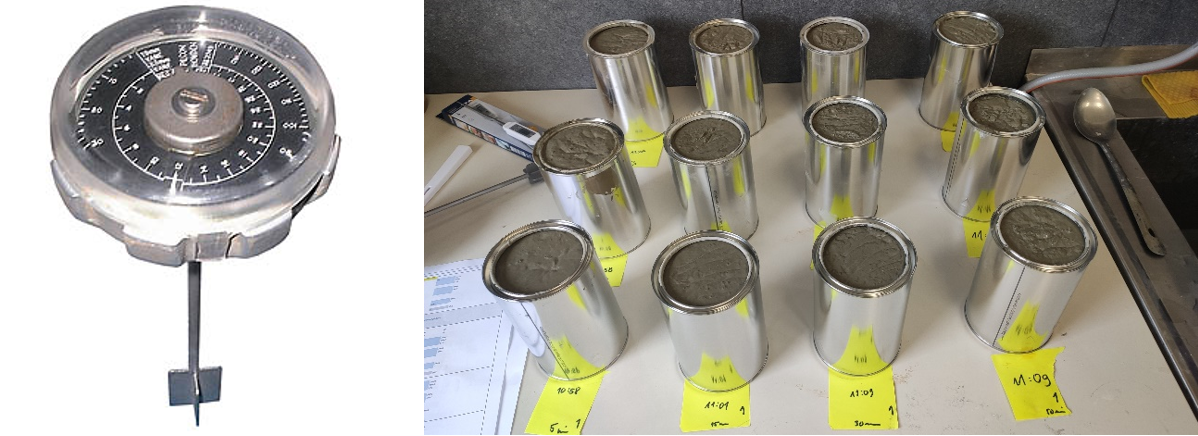
The used hand Vane tester and test cylinders where the Vane device was inserted at specific time intervals.
It’s one thing to learn from presentations, seminars, or scientific articles, but quite another to conduct actual tests, especially those recently introduced. Conducting these tests with together with colleagues from ZAG using their equipment provided valuable learning experience. We’ve gained some new knowledge and intend to incorporate some of these tests into our fresh test routine in the future.